The Regenx Story
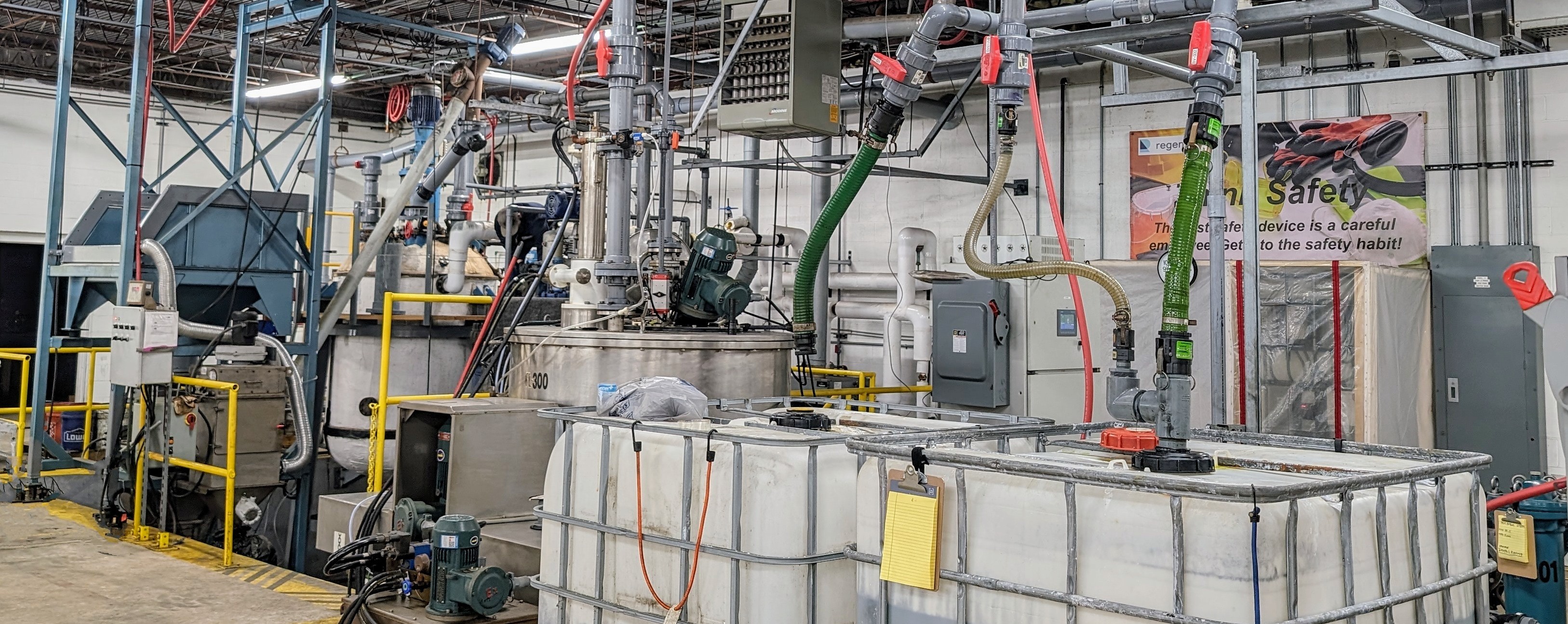
Historically, Regenx was traditional junior mining and exploration company but saw the potential of eco-friendly material processing technologies. The company’s first leap into the cleantech space involved processing old tailing materials with a mobile platform featuring water recycling capabilities. As Regenx advanced its eco-friendly technology, it was approached to adapt its expertise for new materials—first in the e-waste sector and later by Davis Recycling for catalytic converters.
In early 2020, Regenx began laboratory testing on its catalytic converter recycling project. With expertise in materials processing and chemistry, the company has successfully advanced the project from lab testing to pilot plant operations, culminating in commercialization. Today, Regenx is operating Module One at its facility in Eastern Tennessee, which has a design capacity of 5,000 lbs per day. Plans are in place to expand the facility with three additional modules, bringing the full plant capacity to 10 tons per day.
Regenx’s cleantech is leading the way in the Diesel Silicon-Carbide (SiC) converter recycling market, a niche sector with limited recycling options due to smelters facing efficiency issues when processing diesel converters. Stricter environmental regulations have also increased the demand for diesel converters, positioning Regenx to thrive in a growing market where the average converter has a lifespan of approximately 10 to 15 years. With platinum and palladium demand outstripping supply by an average of 259,000 troy ounces annually over the past eight years, and the majority of the supply coming from geopolitically sensitive regions like Russia and South Africa, the U.S. government has identified Platinum Group Metals (PGM) as critical supply minerals. Regenx's innovative process is meeting this demand through sustainable recycling.
The Regenx process starts with purchasing feedstock from suppliers, which is then turned into fine powder by Davis Recycling, Regenx’s operational partner. The powder is treated with Regenx’s proprietary chemistry to extract precious metals, which are further refined into a "Black Powder" concentrate. This concentrate is upgraded to 99.9% purity by a refiner then sold into the commodity markets.
Mining for PGM is capital, energy, and labor-intensive, making increased recycling the only sustainable option to meet growing demand. In 2023, only 35% of the annual PGM demand was met by recycling, despite the fact that over 27 million auto catalysts are scrapped each year. Traditional smelters, which emit approximately 1,500 kg of CO2 for every ton of feedstock processed, face increasing regulatory and environmental challenges, signaling the need for alternative recycling solutions. Regenx is a vital player in the Circular Economy of PGM, offering a process that generates 95% less CO2 emissions and uses 99% less water than traditional mining methods. Its product aligns with manufacturers’ growing demand for eco-friendly, closed-loop production cycles.