Catalytic Converters
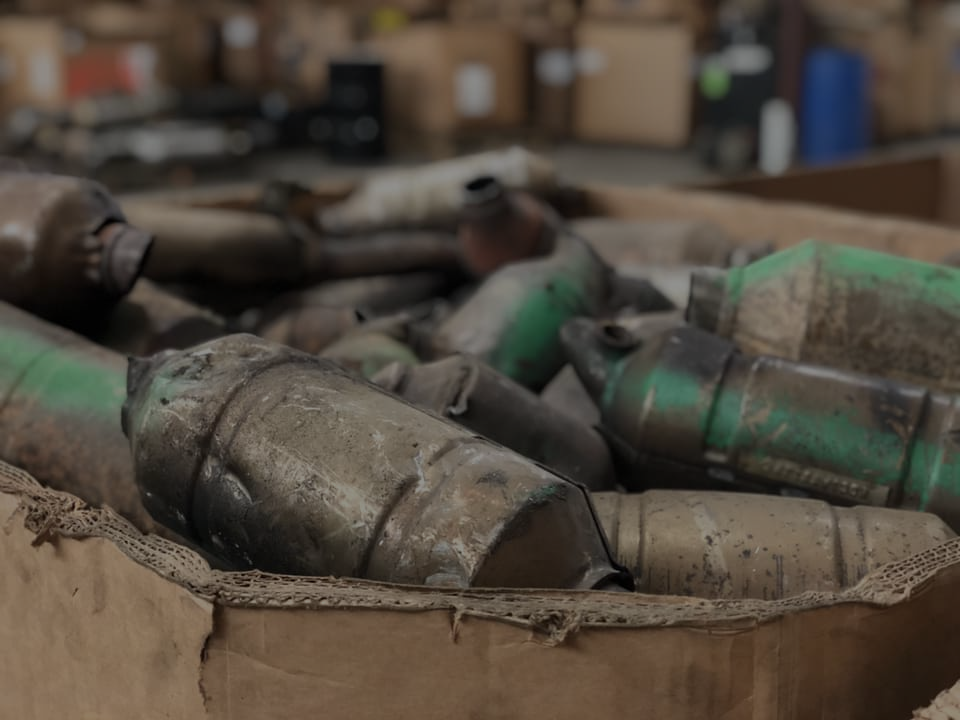
Diesel engines are fundamentally different from gasoline engines. Gas-powered vehicles (vehicles with an Internal Combustion Engine) use a spark to ignite the fuel. Diesel, on the other hand, uses compression to ignite the fuel. This method requires a high air-to-fuel ratio so that there is plenty of oxygen present to ensure total ignition. Emissions from diesel engines are higher in levels of nitrogen oxides and particulate matter, while also exiting the engine at a higher temperature.
A gasoline engine emits hydrocarbons, carbon monoxide, and oxides of nitrogen. This is due to the engine running at an air/fuel ratio of approximately 14.7 to 1, which is the theoretically perfect ratio whereby all the fuel will combust with all of the air and is called the stoichiometric ratio. The methodology required to clean all three of these simultaneously is called a three-way catalytic converter. A three-way catalyst requires the engine to oscillate back and forth between either side of the stoichiometric point. Diesel engines are typically more efficient than gas engines, but this "lean" burning method presents challenges in the catalyst.
Every diesel system will have a Diesel Oxidation Catalyst. It is what converts the carbon monoxide into carbon dioxide and also breaks down any un-spent fuel. Functionally, this aspect of the diesel catalyst system performs just like it does in a gas cat. The DOC is usually the smallest component of a diesel converter, but also the one with the highest recycle value; most of the platinum and palladium is located in this section of the converter. It is almost always the first component in the exhaust system.
Diesel engines produce an extra pollutant that Internal Combustion Engines don't: particulates (or "soot"). The DPF is designed to capture these particulates by making use of a wall-flow monolith, which consists of alternating open/closed channels that allows the particulates to enter the converter from the inlet side, and holds them until they can be broken down and removed by a process called "regeneration". Regeneration is similar to the oxidation process in the DOC, where organic material is burned to produce CO2 and water. To aid in the regeneration step, the DPF is loaded with small amounts of platinum and palladium to help catalyze the reaction. Additionally, the DPF needs to be heated to a high temperature, which will allow the soot to burn up and pass through the filter walls and out the tailpipe. Regeneration is usually controlled by the vehicle's on-board computer.
The SCR catalyst is something that might cause a few converter buyers to raise an eyebrow. This section of the diesel converter is typically the largest, and yet it has very little recycle value. This is the component that carries out the reduction of the NOx gases. In a three-way converter, Rhodium is the precious metal that catalyzes the reduction reaction; which converts NOx into nitrogen gas and oxygen. However, because of the high-oxygen content of diesel exhaust, Rhodium cannot efficiently reduce the NOx gases in a diesel converter. Therefore, diesel converters typically DO NOT contain rhodium. Instead, the SCR makes use of an additive called "diesel exhaust fluid" (DEF), which is made up of either ammonia or urea. The ceramic monolith still contains catalytic materials, but they usually have no recycling value. The DEF, along with catalytic materials, are able to adequately remove the NOx from the exhaust. Some SCR catalysts contain a small section near the back of the biscuit called the "ammonia slip catalyst", which contains a small amount of platinum. Its purpose is to burn off any excess ammonia from the DEF. Typically, the amount of platinum is so small on this section that it is not cost-effective to recycle it. Another method of reducing NOx in a diesel system is a process called Exhaust Gas Re-circulation. This process doesn't require an SCR catalyst or DEF, so not all diesel vehicles will necessarily have an SCR biscuit. The SCR and the DPF are always downstream of the DOC, but the position of either of them can be swapped.
In catalytic converters available on the market, there are two main types of material cordierite and silicon carbide (SiC). Cordierite is a ceramic material that provides good filtration of pollution particles and is economical to produce. SiC is a material that offers better filtration quality, greater thermal resistance and a much longer service life. As diesel engines generally operate at higher temperatures so utilize SiC for the substrate. The SiC require an alternate smelting atmosphere than regular gasoline converters, otherwise a distortion will be present in the separation of precious metals that muck up the process. It slows down processing, forcing systems to be purged and cleaned more frequently. Most smelters don’t want the SiC material and as a result charge higher fees impacting payouts, plus higher processing fees.